Manutenção industrial e caldeiraria: práticas e benefícios essenciais
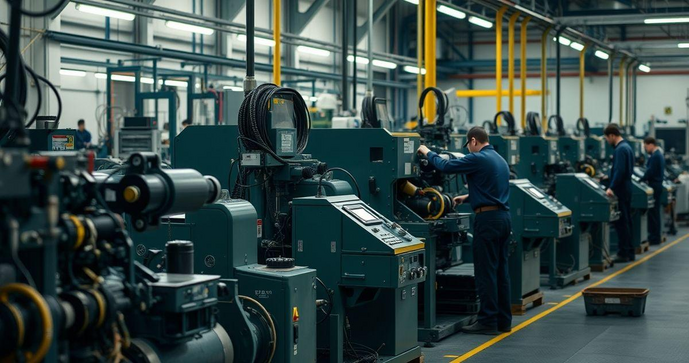
Por: Gabriel - 30 de Abril de 2025
Importância da Manutenção Industrial na Eficiência Operacional
A manutenção industrial é um fator chave para a eficiência operacional nas empresas. Ao garantir que os equipamentos estejam sempre em condições ideais de funcionamento, as indústrias conseguem evitar paradas inesperadas que podem afetar a produção e gerar custos elevados.
Um dos principais objetivos da manutenção industrial é maximizar a disponibilidade dos maquinários. Quando as máquinas estão em perfeito estado, a produtividade aumenta significativamente. Por exemplo, uma manutenção programada pode prevenir falhas que, se não tratadas, resultariam em interrupções no fluxo de trabalho.
A redução de custos também é um benefício significativo da manutenção adequada. Através de práticas de manutenção preventiva, as empresas evitam reparos emergenciais, que costumam ser mais caros e exigem tempo adicional para a solução dos problemas. Além disso, a manutenção regular contribui para a vida útil dos equipamentos, retardando a necessidade de substituição.
Outra questão importante é a segurança do ambiente de trabalho. Equipamentos mal mantidos podem representar riscos potenciais aos colaboradores. Ao realizar manutenções regulares, as indústrias garantem não apenas a segurança dos operadores, mas também a conformidade com normas de segurança e regulamentações vigentes.
Finalmente, a manutenção industrial pode fomentar uma cultura de melhoria contínua dentro das organizações. Quando as equipes são treinadas para realizar manutenções regulares e a importância disso é enfatizada, todos se tornam mais conscientes em relação ao cuidado com os equipamentos, resultando em um ambiente de trabalho mais eficiente e produtivo.
Principais Tipos de Manutenção em Caldeiraria
A caldeiraria é uma área crucial na indústria, e a manutenção adequada dos equipamentos é fundamental para garantir a segurança e a eficiência.
Existem vários tipos de manutenção que podem ser aplicados em caldeiras e outros componentes industriais.
Abaixo, destacamos os principais tipos de manutenção em caldeiraria:
1. Manutenção Preventiva: Este tipo de manutenção é realizado regularmente para identificar e corrigir problemas antes que se tornem falhas.
A manutenção preventiva inclui inspeções programadas, limpeza e ajustes nos equipamentos, o que ajuda a prolongar a vida útil das caldeiras.
2. Manutenção Corretiva: A manutenção corretiva é realizada após a detecção de falhas ou irregularidades no funcionamento do equipamento.
Ela visa restaurar o funcionamento normal das caldeiras, desenvolvendo reparos necessários.
Essa modalidade pode resultar em paradas não planejadas, impactando a produtividade.
3. Manutenção Preditiva: Utilizando tecnologias como análises de vibrações, termografia e medições de desgaste, a manutenção preditiva permite monitorar o estado dos equipamentos em tempo real.
Assim, é possível prever falhas antes que ocorram, permitindo a programação de intervenções com menos interrupções na produção.
4. Manutenção Sistemática: Também chamada de manutenção programada, este tipo envolve a aplicação de um cronograma de trabalhos que visa garantir a operacionalidade dos equipamentos ao longo de um período determinado.
Em caldeiraria, isso pode incluir testes de pressão e inspeções de segurança exigidos por normas regulamentadoras.
5. Manutenção de Emergência: Esta manutenção é necessária em situações críticas, quando uma falha inesperada acontece.
É geralmente a forma mais custosa de manutenção, pois leva a interrupções brutas na operação, e exige intervenções imediatas para corrigir o problema e restaurar as condições operacionais.
Ao utilizar uma combinação desses tipos de manutenção, as indústrias podem maximizar a eficiência e a segurança dos seus sistemas de caldeiraria, minimizando riscos e custos associados a falhas e paradas não planejadas.
Benefícios da Manutenção Preventiva em Equipamentos Industriais
A manutenção preventiva é uma prática essencial em ambientes industriais, trazendo múltiplos benefícios para a operação dos equipamentos. Este tipo de manutenção consiste em ações programadas realizadas periodicamente, com o objetivo de manter a funcionalidade e a segurança dos maquinários. A seguir, destacamos alguns dos principais benefícios da manutenção preventiva em equipamentos industriais:
1. Aumento da Disponibilidade: Com a manutenção preventiva, as máquinas são mantidas em condições ideais de operação. Isso resulta em uma maior disponibilidade dos equipamentos, reduzindo o tempo de inatividade e aumentando a produtividade da linha de produção.
2. Redução de Custos: Investir em manutenção preventiva pode parecer um custo adicional, mas, na realidade, ajuda a evitar despesas mais elevadas relacionadas a reparos emergenciais e substituições de equipamentos. A identificação e correção de problemas antes que se agravem economiza dinheiro a longo prazo.
3. Prolongamento da Vida Útil dos Equipamentos: Equipamentos que recebem manutenção preventiva tendem a ter uma vida útil mais longa. Cuidados regulares, como lubrificação, limpeza e ajustes, garantem que os componentes funcionem de maneira eficiente, prevenindo desgaste excessivo.
4. Aumento da Segurança: A manutenção preventiva não só mantém as máquinas funcionando corretamente, mas também garante a segurança dos trabalhadores. A realização de inspeções periódicas ajuda a identificar riscos potenciais e a mitigar acidentes, resultando em um ambiente de trabalho mais seguro.
5. Melhoria na Qualidade do Produto: Equipamentos bem mantidos produzem melhor qualidade, pois operam de forma eficiente e consistem de medições corretas. Isso é crucial em indústrias onde a qualidade do produto final é primordial.
6. Conformidade com Normas: Muitos setores industriais são regidos por normas de segurança que requerem a manutenção regular dos equipamentos. A manutenção preventiva ajuda a garantir que as empresas estejam em conformidade, evitando penalidades e melhorando sua reputação no mercado.
Por fim, a implementação de um programa de manutenção preventiva é uma estratégia inteligente para maximizar a eficiência operacional e minimizar riscos em ambientes industriais. Investir nessa prática resulta em um ciclo virtuoso de manutenção, onde os equipamentos operam com a máxima eficiência.
Técnicas Modernas de Manutenção em Caldeiras
As técnicas modernas de manutenção em caldeiras têm evoluído significativamente com o avanço da tecnologia, proporcionando métodos mais eficazes e eficientes para garantir a segurança e a operação contínua desses equipamentos essenciais. Abaixo, estão algumas das técnicas mais relevantes que têm sido adotadas na manutenção de caldeiras:
1. Monitoramento em Tempo Real: O uso de sensores e sistemas de monitoramento em tempo real permite que as indústrias acompanhem o desempenho das caldeiras continuamente. Dados como pressão, temperatura e fluxo de vapor são analisados constantemente, possibilitando a identificação imediata de anomalias.
2. Análise Preditiva: Com a incorporação de técnicas de análise preditiva, é possível prever falhas antes que ocorram. Utilizando algoritmos avançados e aprendizado de máquina, as indústrias conseguem avaliar o estado dos equipamentos e agendar manutenções nos momentos mais apropriados, evitando paradas não planejadas.
3. Tecnologia de Termografia: Esta técnica envolve o uso de câmeras infravermelhas para detectar anomalias térmicas nas caldeiras. A termografia ajuda a identificar áreas de superaquecimento ou falhas de isolamento, que podem causar danos significativos se não forem corrigidos rapidamente.
4. Ultrassom para Detecção de Vazamentos: O uso de tecnologia ultrassônica permite a detecção precoce de vazamentos em caldeiras. Essa técnica é non-invasive e pode ser realizada sem necessidade de desligar o equipamento, o que minimiza interrupções na operação.
5. Inspeções Robóticas: Veículos robóticos são cada vez mais utilizados para realizar inspeções internas em caldeiras. Equipados com câmeras e dispositivos sensoriais, esses robôs podem acessar áreas de difícil alcance e fornecer dados valiosos sobre a condição interna do equipamento.
6. Manutenção Baseada em Condição: Essa abordagem permite que a manutenção seja realizada com base na condição real da caldeira em vez de um cronograma fixo. Isso é feito por meio de monitoramento contínuo e análises de dados, garantindo que as intervenções ocorram somente quando necessário.
Essas técnicas modernas de manutenção não apenas aumentam a eficiência operacional das caldeiras, mas também asseguram um ambiente de trabalho mais seguro e econômico. A adoção dessas tecnologias e práticas inovadoras resulta em custo-benefício a longo prazo, criando um ciclo de manutenção mais sustentável e responsável.
Normas e Regulamentações para Caldeiraria Industrial
As normas e regulamentações para caldeiraria industrial são fundamentais para garantir a segurança e a eficiência dos sistemas de caldeiras e equipamentos relacionados. Essas diretrizes têm como objetivo proteger não apenas as instalações industriais, mas também os trabalhadores e o meio ambiente. A seguir, apresentamos algumas das principais normas e regulamentações que regem a caldeiraria:
1. Normas da ABNT (Associação Brasileira de Normas Técnicas): A ABNT estabelece normas técnicas específicas para a fabricação, inspeção e manutenção de caldeiras. Entre as normas mais relevantes, destaca-se a NBR 13.596, que aborda critérios gerais para caldeiras industriais, estabelecendo requisitos de segurança e desempenho.
2. NR-13 (Norma Regulamentadora 13): Esta norma, vinculada ao Ministério do Trabalho e Emprego, regulamenta a segurança na operação de caldeiras e vasos de pressão. Ela define requisitos para inspeção, manutenção e operação segura, visando a proteção dos trabalhadores e a integridade dos equipamentos.
3. ASME (American Society of Mechanical Engineers): Embora seja uma norma internacional, vários setores industriais no Brasil adotam as diretrizes da ASME para a fabricação e operação de caldeiras. As normas ASME estabelecem padrões rigorosos para garantir a segurança operacional e a confiabilidade dos equipamentos.
4. Normas ISO: A implementação de normas ISO, como a ISO 9001 (qualidade) e ISO 14001 (gestão ambiental), é comum nas indústrias que operam com caldeiras. Essas certificações ajudam a promover práticas de gestão sustentável e qualidade no controle dos processos industriais.
5. Normas de Segurança e Meio Ambiente: Diversas regulamentações ambientais também impactam as operações de caldeiraria, como a Lei de Poluição Ambiental (Lei nº 9.605/98). As indústrias precisam garantir que suas operações atendam a critérios ambientais, evitando danos ao meio ambiente e possíveis sanções legais.
6. Normas de Inspeção e Teste: As caldeiras devem passar por inspeções regulares e testes de pressão, conforme estabelecido por normas específicas. Essa prática assegura que os equipamentos operem dentro dos limites de segurança, prevenindo falhas e acidentes.
A conformidade com essas normas e regulamentações é essencial para a operação segura e eficaz das caldeiras industriais. As indústrias devem estar sempre atualizadas em relação às exigências regulatórias, garantindo que suas práticas operacionais protejam os trabalhadores, os equipamentos e o meio ambiente.
Desafios e Soluções em Projetos de Manutenção Industrial
Os projetos de manutenção industrial enfrentam diversos desafios que podem comprometer a eficiência e a segurança das operações. Reconhecer esses obstáculos e desenvolver soluções adequadas é fundamental para uma gestão eficaz. A seguir, apresentamos alguns dos principais desafios e suas respectivas soluções:
1. Falta de Planejamento Adequado: Um dos principais desafios em projetos de manutenção é a ausência de um planejamento estruturado. Isso pode levar a falhas na execução das atividades. Solução: Implementar um sistema de gerenciamento de manutenção (GMAO) que permita programar intervencionais, monitorar o desempenho e otimizar o uso de recursos.
2. Escassez de Mão de Obra Qualificada: A falta de profissionais capacitados pode afetar a qualidade da manutenção e aumentar o tempo de inatividade dos equipamentos. Solução: Promover treinamento contínuo para a equipe e atrair novos talentos por meio de parcerias com instituições de ensino técnico e superior.
3. Alta Carga de Trabalho: A demanda excessiva de tarefas pode resultar em priorização inadequada das atividades de manutenção, levando a problemas de segurança. Solução: Implementar uma estratégia de manutenção equilibrada, utilizando dados de análise preditiva para priorizar atividades e garantir um fluxo de trabalho sustentável.
4. Integração de Novas Tecnologias: A integração de novas tecnologias e ferramentas de monitoramento pode ser desafiadora, especialmente em indústrias com sistemas legados. Solução: Realizar uma avaliação sistemática das tecnologias disponíveis e desenvolver um plano de implementação gradual que minimize riscos e maximize a integração.
5. Conformidade com Normas e Regulações: Manter conformidade com as regulamentações de segurança e ambientais pode ser complexo e demandar recursos significativos. Solução: Criar uma equipe dedicada à conformidade que monitore as atualizações nas normas e desenvolva práticas para garantir que todos os processos operacionais estejam em conformidade.
6. Orçamentos Limitados: Muitas vezes, os projetos de manutenção enfrentam restrições orçamentárias, o que pode limitar a capacidade de realizar manutenções adequadas. Solução: Realizar uma análise de custo-benefício para priorizar investimentos em manutenção e buscar alternativas de financiamento, como contratos de manutenção com fornecedores.
Ao abordar esses desafios com soluções estratégicas, as indústrias podem melhorar a eficácia de seus projetos de manutenção, garantindo operações mais seguras e eficientes. Adotar uma mentalidade proativa em relação à manutenção é essencial para minimizar riscos e maximizar a durabilidade dos equipamentos.
A manutenção industrial, especialmente no contexto da caldeiraria, é uma disciplina essencial que garante a segurança e a eficiência operacional das indústrias. Por meio da implementação de práticas como a manutenção preventiva, o acompanhamento das normas e regulamentações, e a adoção de técnicas modernas, as empresas podem enfrentar os desafios comuns e assegurar o funcionamento contínuo de seus equipamentos.
Com a atenção voltada para as melhores práticas de manutenção, é possível reduzir custos, aumentar a produtividade e garantir um ambiente de trabalho seguro para todos os colaboradores. Investir em manutenção não é apenas uma questão de conformidade com as normas, mas sim uma estratégia indispensável para o sucesso a longo prazo de qualquer operação industrial.