Manutenção e instalação industrial: soluções completas para empresas
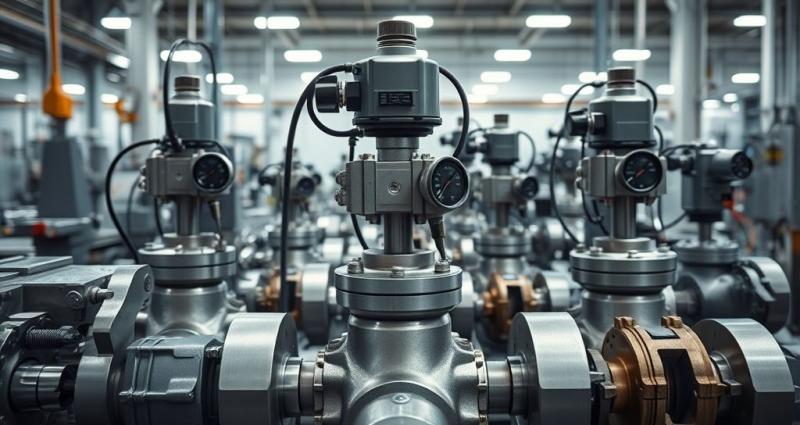
Por: Gabriel - 30 de Abril de 2025
A manutenção e instalação industrial desempenham um papel crucial na eficiência e segurança das operações em ambientes produtivos. Com o aumento da complexidade dos equipamentos e a necessidade de maximizar a produtividade, entender as melhores práticas para a manutenção e instalação se torna essencial. Neste artigo, abordaremos a importância desses processos, oferecendo dicas e orientações para garantir que sua instalação industrial funcione de maneira otimizada e segura.
Importância da Manutenção Preventiva em Ambientes Industriais
A manutenção preventiva é uma estratégia fundamental para garantir a eficiência e a segurança em ambientes industriais. Ao contrário da manutenção corretiva, que é realizada após a ocorrência de falhas, a manutenção preventiva visa identificar e corrigir problemas antes que eles se tornem críticos. Essa abordagem não apenas prolonga a vida útil dos equipamentos, mas também minimiza o tempo de inatividade e os custos operacionais.
Um dos principais benefícios da manutenção preventiva é a redução de falhas inesperadas. Em um ambiente industrial, onde a produção é contínua e a eficiência é crucial, uma falha em um equipamento pode resultar em paradas significativas, afetando toda a linha de produção. Ao implementar um programa de manutenção preventiva, as empresas podem realizar inspeções regulares e manutenções programadas, garantindo que os equipamentos estejam sempre em condições ideais de funcionamento.
Além disso, a manutenção preventiva contribui para a segurança dos trabalhadores. Equipamentos mal mantidos podem representar riscos sérios, como acidentes e lesões. Por exemplo, uma máquina que não passa por verificações regulares pode apresentar falhas que coloquem em risco a integridade física dos operadores. Ao garantir que todos os equipamentos estejam em conformidade com as normas de segurança, as empresas não apenas protegem seus funcionários, mas também evitam possíveis processos legais e danos à reputação.
Outro aspecto importante da manutenção preventiva é a otimização dos custos operacionais. Embora possa parecer um investimento inicial significativo, a manutenção regular pode resultar em economias substanciais a longo prazo. Equipamentos bem mantidos consomem menos energia e têm um desempenho mais eficiente, o que se traduz em menores custos operacionais. Além disso, a redução do tempo de inatividade significa que a produção pode continuar sem interrupções, aumentando a produtividade geral da empresa.
As empresas que adotam a manutenção preventiva também se beneficiam de um melhor planejamento orçamentário. Com um programa de manutenção bem estruturado, é possível prever e alocar recursos financeiros para as atividades de manutenção, evitando surpresas financeiras. Isso permite que as empresas mantenham um fluxo de caixa mais estável e planejem investimentos futuros com mais segurança.
Um exemplo prático da importância da manutenção preventiva pode ser observado em indústrias que utilizam maquinário pesado. Equipamentos como guindastes, prensas e fornos requerem manutenção regular para garantir que operem de maneira segura e eficiente. A falta de manutenção pode levar a falhas catastróficas, resultando em custos elevados de reparo e, em alguns casos, até mesmo na necessidade de substituição do equipamento. Portanto, a manutenção preventiva se torna uma estratégia essencial para proteger o investimento em maquinário e garantir a continuidade das operações.
Além disso, a manutenção preventiva pode ser integrada a sistemas de gestão de manutenção assistida por computador (CMMS), que ajudam a monitorar o desempenho dos equipamentos e a programar manutenções de forma mais eficiente. Esses sistemas permitem que as empresas acompanhem o histórico de manutenção, identifiquem tendências e ajustem suas estratégias conforme necessário. A tecnologia, portanto, desempenha um papel vital na implementação de práticas de manutenção preventiva eficazes.
Outro ponto a ser considerado é a importância da formação e capacitação dos funcionários. Para que a manutenção preventiva seja eficaz, é fundamental que os trabalhadores estejam bem treinados e cientes das práticas de segurança. Investir em treinamentos regulares não apenas melhora a eficiência da manutenção, mas também promove uma cultura de segurança dentro da empresa. Funcionários bem informados são mais propensos a identificar problemas potenciais e a relatar falhas antes que se tornem críticas.
Por fim, a escolha de uma Empresa de montagem industrial confiável pode fazer toda a diferença na implementação de um programa de manutenção preventiva. Profissionais experientes podem oferecer orientações valiosas sobre as melhores práticas e ajudar a desenvolver um plano de manutenção adaptado às necessidades específicas da sua operação. Com o suporte adequado, as empresas podem maximizar os benefícios da manutenção preventiva e garantir um ambiente de trabalho seguro e eficiente.
Em resumo, a manutenção preventiva é uma prática essencial em ambientes industriais, proporcionando segurança, eficiência e economia. Ao investir em manutenção regular, as empresas não apenas protegem seus ativos, mas também garantem a continuidade das operações e a segurança de seus colaboradores. A implementação de um programa de manutenção preventiva bem estruturado é, portanto, uma estratégia inteligente para qualquer organização que busca se destacar em um mercado competitivo.
Passo a Passo para uma Instalação Industrial Eficiente
A instalação industrial é um processo complexo que requer planejamento cuidadoso e execução precisa. Uma instalação bem-sucedida não apenas garante a funcionalidade dos equipamentos, mas também contribui para a segurança e eficiência das operações. A seguir, apresentamos um passo a passo para realizar uma instalação industrial eficiente, abordando desde o planejamento até a execução e a verificação final.
1. Planejamento da Instalação
O primeiro passo para uma instalação industrial eficiente é o planejamento. É fundamental definir claramente os objetivos da instalação, os equipamentos que serão utilizados e o layout do espaço. Um bom planejamento deve incluir a análise do fluxo de trabalho, a disposição dos equipamentos e a identificação de possíveis obstáculos. Além disso, é importante considerar as normas de segurança e regulamentações aplicáveis ao setor.
Durante essa fase, é aconselhável consultar especialistas e engenheiros que possam oferecer insights valiosos sobre o projeto. Eles podem ajudar a identificar as melhores práticas e garantir que todos os aspectos técnicos sejam considerados. O planejamento adequado é a base para uma instalação bem-sucedida e pode evitar problemas futuros.
2. Escolha dos Materiais e Equipamentos
A escolha dos materiais e equipamentos é um aspecto crucial da instalação industrial. É importante optar por produtos de alta qualidade que atendam às necessidades específicas da operação. Por exemplo, se a instalação envolver a manipulação de substâncias corrosivas, é essencial utilizar materiais resistentes, como aço inoxidável. Para isso, é recomendável buscar uma Distribuidora de aço inox confiável que ofereça produtos de qualidade e suporte técnico.
Além disso, a escolha dos equipamentos deve levar em consideração a capacidade de produção, a eficiência energética e a compatibilidade com outros sistemas existentes. Realizar uma pesquisa de mercado e comparar diferentes fornecedores pode ajudar a encontrar as melhores opções disponíveis.
3. Preparação do Local de Instalação
Antes de iniciar a instalação, é fundamental preparar o local adequadamente. Isso inclui a limpeza do espaço, a remoção de obstruções e a verificação das condições elétricas e hidráulicas. É importante garantir que todas as instalações elétricas estejam em conformidade com as normas de segurança e que haja acesso adequado a fontes de energia.
Além disso, a área de instalação deve ser organizada de forma a facilitar o trabalho da equipe. Ter todas as ferramentas e materiais necessários à mão pode acelerar o processo e minimizar interrupções. A segurança deve ser uma prioridade durante essa fase, e todos os trabalhadores devem estar cientes das práticas de segurança a serem seguidas.
4. Execução da Instalação
Com o planejamento e a preparação concluídos, é hora de executar a instalação. É importante seguir as instruções do fabricante para cada equipamento e garantir que todas as etapas sejam realizadas de acordo com as especificações. A equipe de instalação deve ser composta por profissionais qualificados e experientes, que entendam os requisitos técnicos e de segurança.
Durante a instalação, é fundamental realizar verificações regulares para garantir que tudo esteja sendo montado corretamente. Isso inclui a verificação de alinhamentos, conexões elétricas e a integridade dos materiais utilizados. A comunicação entre os membros da equipe é essencial para garantir que todos estejam cientes do progresso e de quaisquer problemas que possam surgir.
5. Testes e Verificações Finais
Após a conclusão da instalação, é crucial realizar testes e verificações finais. Isso envolve a execução de testes de funcionamento para garantir que todos os equipamentos operem conforme o esperado. Verifique se há vazamentos, ruídos anormais ou qualquer outro sinal de que algo não está funcionando corretamente.
Além disso, é importante revisar as configurações de segurança e garantir que todos os dispositivos de proteção estejam funcionando adequadamente. A realização de uma inspeção final pode ajudar a identificar problemas que não foram detectados durante a instalação e garantir que tudo esteja em conformidade com as normas de segurança.
6. Treinamento da Equipe
Uma instalação industrial eficiente não termina com a montagem dos equipamentos. É fundamental que a equipe que operará os sistemas receba treinamento adequado. Isso inclui instruções sobre o funcionamento dos equipamentos, procedimentos de segurança e práticas de manutenção. Um bom treinamento pode aumentar a eficiência operacional e reduzir o risco de acidentes.
Além disso, é importante estabelecer um plano de manutenção preventiva para garantir que os equipamentos permaneçam em boas condições ao longo do tempo. A manutenção regular pode ajudar a evitar falhas e prolongar a vida útil dos equipamentos, contribuindo para a eficiência da operação.
7. Avaliação e Melhoria Contínua
Por fim, após a instalação e o treinamento, é importante realizar uma avaliação do processo. Isso envolve a coleta de feedback da equipe e a análise do desempenho dos equipamentos. Identificar áreas de melhoria pode ajudar a otimizar futuras instalações e garantir que a operação continue a evoluir.
Em resumo, a instalação industrial eficiente requer um planejamento cuidadoso, a escolha adequada de materiais e equipamentos, preparação do local, execução precisa, testes finais, treinamento da equipe e avaliação contínua. Seguir esse passo a passo pode garantir que a instalação atenda às necessidades da operação e contribua para a segurança e eficiência do ambiente industrial.
Principais Equipamentos que Requerem Manutenção Regular
A manutenção regular de equipamentos industriais é essencial para garantir a eficiência, segurança e longevidade das operações. Diversos tipos de equipamentos são utilizados em ambientes industriais, e cada um deles possui características específicas que demandam cuidados regulares. A seguir, apresentamos uma lista dos principais equipamentos que requerem manutenção regular e as práticas recomendadas para cada um deles.
1. Máquinas de Corte e Soldagem
As máquinas de corte e soldagem são fundamentais em muitos processos industriais, especialmente em setores como a Caldeiraria e montagem industrial. Esses equipamentos exigem manutenção regular para garantir que funcionem de maneira eficiente e segura. A manutenção deve incluir a verificação de componentes como lâminas, eletrodos e sistemas de refrigeração.
Além disso, é importante realizar limpezas periódicas para remover resíduos de solda e sujeira que podem afetar o desempenho da máquina. A calibração dos equipamentos também deve ser feita regularmente para garantir cortes precisos e soldas de qualidade. Ignorar a manutenção dessas máquinas pode resultar em falhas, desperdício de material e riscos de segurança.
2. Compressores de Ar
Os compressores de ar são amplamente utilizados em diversas indústrias para fornecer ar comprimido a ferramentas pneumáticas e sistemas de automação. A manutenção regular é crucial para garantir que esses equipamentos operem de forma eficiente. Isso inclui a verificação de filtros, lubrificação de componentes móveis e inspeção de mangueiras e conexões.
Os filtros de ar devem ser limpos ou substituídos regularmente para evitar a contaminação do ar comprimido. Além disso, a verificação de vazamentos é essencial, pois vazamentos podem resultar em perda de eficiência e aumento nos custos operacionais. A manutenção preventiva dos compressores de ar pode evitar falhas inesperadas e prolongar a vida útil do equipamento.
3. Bombas
As bombas são equipamentos críticos em muitos processos industriais, sendo responsáveis pelo transporte de líquidos e gases. A manutenção regular das bombas é vital para garantir seu funcionamento adequado. Isso inclui a verificação de vedações, rolamentos e sistemas de acionamento.
É importante monitorar o desempenho da bomba e realizar ajustes conforme necessário. A lubrificação adequada dos componentes móveis e a limpeza de filtros são práticas recomendadas que ajudam a evitar falhas. Além disso, a inspeção de mangueiras e conexões é essencial para prevenir vazamentos e garantir a segurança do sistema.
4. Motores Elétricos
Os motores elétricos são a força motriz por trás de muitos equipamentos industriais, e sua manutenção regular é crucial para garantir a eficiência operacional. A manutenção deve incluir a verificação de conexões elétricas, limpeza de componentes e lubrificação de rolamentos.
Além disso, é importante monitorar a temperatura de operação do motor e realizar testes de vibração para identificar possíveis problemas. A manutenção preventiva dos motores elétricos pode evitar falhas catastróficas e garantir que os equipamentos funcionem de maneira contínua e eficiente.
5. Sistemas de Ventilação e Exaustão
Os sistemas de ventilação e exaustão são essenciais para manter a qualidade do ar em ambientes industriais. A manutenção regular desses sistemas é fundamental para garantir que funcionem de maneira eficaz. Isso inclui a limpeza de filtros, verificação de dutos e inspeção de ventiladores.
Os filtros devem ser limpos ou substituídos regularmente para garantir que o ar circulante esteja livre de contaminantes. Além disso, a verificação de vazamentos nos dutos é essencial para garantir a eficiência do sistema. A manutenção adequada dos sistemas de ventilação e exaustão não apenas melhora a qualidade do ar, mas também contribui para a segurança dos trabalhadores.
6. Equipamentos de Segurança
Os equipamentos de segurança, como extintores de incêndio, sistemas de alarme e equipamentos de proteção individual (EPIs), também requerem manutenção regular. A verificação e a manutenção desses equipamentos são essenciais para garantir a segurança dos trabalhadores e a conformidade com as normas de segurança.
Os extintores de incêndio devem ser inspecionados periodicamente para garantir que estejam em condições de uso. Os sistemas de alarme devem ser testados regularmente para garantir que funcionem corretamente em caso de emergência. Além disso, os EPIs devem ser verificados quanto a danos e substituídos conforme necessário para garantir a proteção dos trabalhadores.
7. Sistemas Hidráulicos
Os sistemas hidráulicos são amplamente utilizados em equipamentos pesados e maquinário industrial. A manutenção regular desses sistemas é crucial para garantir seu funcionamento adequado. Isso inclui a verificação de fluidos hidráulicos, vedações e mangueiras.
É importante monitorar o nível de fluido hidráulico e realizar trocas regulares para garantir que o sistema opere de maneira eficiente. A inspeção de vedações e mangueiras é essencial para prevenir vazamentos e garantir a segurança do sistema. A manutenção preventiva dos sistemas hidráulicos pode evitar falhas e prolongar a vida útil do equipamento.
Em resumo, a manutenção regular de equipamentos industriais é essencial para garantir a eficiência, segurança e longevidade das operações. Máquinas de corte e soldagem, compressores de ar, bombas, motores elétricos, sistemas de ventilação, equipamentos de segurança e sistemas hidráulicos são apenas alguns dos equipamentos que requerem cuidados regulares. Implementar um programa de manutenção preventiva pode ajudar a evitar falhas, reduzir custos operacionais e garantir um ambiente de trabalho seguro e eficiente.
Erros Comuns na Instalação e Como Evitá-los
A instalação de equipamentos industriais é uma etapa crítica que pode determinar o sucesso ou o fracasso de uma operação. Embora a maioria das empresas se esforce para garantir que a instalação seja realizada corretamente, erros podem ocorrer e levar a problemas significativos. A seguir, discutiremos alguns dos erros mais comuns na instalação e como evitá-los, garantindo que sua operação funcione de maneira eficiente e segura.
1. Falta de Planejamento Adequado
Um dos erros mais frequentes na instalação industrial é a falta de planejamento adequado. Muitas vezes, as empresas iniciam a instalação sem um plano claro, o que pode resultar em confusões e retrabalhos. Para evitar esse erro, é fundamental elaborar um plano detalhado que inclua o layout do espaço, a disposição dos equipamentos e as etapas do processo de instalação.
O planejamento deve envolver a análise do fluxo de trabalho e a identificação de possíveis obstáculos. Consultar especialistas e engenheiros durante essa fase pode ajudar a garantir que todos os aspectos técnicos sejam considerados. Um planejamento bem estruturado é a base para uma instalação bem-sucedida.
2. Escolha Inadequada de Materiais e Equipamentos
A escolha inadequada de materiais e equipamentos é outro erro comum que pode comprometer a instalação. É essencial selecionar produtos que atendam às necessidades específicas da operação. Por exemplo, em projetos de Caldeiraria industrial, o uso de materiais de baixa qualidade pode resultar em falhas estruturais e comprometer a segurança.
Para evitar esse erro, é recomendável realizar uma pesquisa de mercado e comparar diferentes fornecedores. Escolher materiais de alta qualidade e equipamentos que sejam compatíveis com os sistemas existentes pode evitar problemas futuros e garantir a durabilidade da instalação.
3. Ignorar Normas de Segurança
Ignorar as normas de segurança durante a instalação é um erro que pode ter consequências graves. A segurança deve ser uma prioridade em todas as etapas do processo de instalação. Isso inclui garantir que todos os equipamentos estejam em conformidade com as regulamentações de segurança e que a equipe esteja ciente das práticas de segurança a serem seguidas.
Para evitar esse erro, é importante realizar treinamentos regulares com a equipe e garantir que todos os trabalhadores estejam cientes das normas de segurança aplicáveis. Além disso, a realização de inspeções de segurança antes, durante e após a instalação pode ajudar a identificar e corrigir problemas antes que se tornem críticos.
4. Falta de Comunicação entre a Equipe
A falta de comunicação entre os membros da equipe é um erro que pode levar a mal-entendidos e falhas na instalação. A comunicação eficaz é essencial para garantir que todos estejam cientes do progresso e das responsabilidades de cada um. Quando a comunicação falha, é mais provável que erros ocorram.
Para evitar esse problema, é importante estabelecer canais de comunicação claros e realizar reuniões regulares para discutir o progresso da instalação. Incentivar a equipe a compartilhar informações e relatar problemas pode ajudar a garantir que todos estejam na mesma página e que a instalação seja concluída com sucesso.
5. Não Realizar Testes e Verificações Finais
Após a conclusão da instalação, muitos profissionais cometem o erro de não realizar testes e verificações finais. Essa etapa é crucial para garantir que todos os equipamentos estejam funcionando corretamente e que não haja problemas ocultos. Ignorar essa fase pode resultar em falhas inesperadas e custos adicionais.
Para evitar esse erro, é fundamental realizar testes de funcionamento e inspeções detalhadas após a instalação. Verifique se todos os sistemas estão operando conforme o esperado e se há vazamentos, ruídos anormais ou qualquer outro sinal de que algo não está funcionando corretamente. A realização de uma inspeção final pode ajudar a identificar problemas que não foram detectados durante a instalação.
6. Subestimar a Importância do Treinamento
Subestimar a importância do treinamento da equipe é um erro que pode comprometer a operação a longo prazo. Mesmo que a instalação tenha sido realizada corretamente, se a equipe não estiver adequadamente treinada para operar os equipamentos, isso pode levar a erros e falhas.
Para evitar esse problema, é essencial investir em treinamentos regulares para a equipe. Isso inclui instruções sobre o funcionamento dos equipamentos, procedimentos de segurança e práticas de manutenção. Um bom treinamento pode aumentar a eficiência operacional e reduzir o risco de acidentes.
7. Não Documentar o Processo de Instalação
A falta de documentação do processo de instalação é um erro que pode causar problemas no futuro. A documentação é essencial para garantir que todas as etapas da instalação sejam registradas e que haja um histórico do que foi feito. Isso pode ser útil para futuras manutenções e para resolver problemas que possam surgir.
Para evitar esse erro, é importante manter registros detalhados de todas as etapas da instalação, incluindo materiais utilizados, configurações e ajustes realizados. Essa documentação pode ser valiosa para a equipe de manutenção e para futuras instalações.
Em resumo, evitar erros comuns na instalação industrial é fundamental para garantir a eficiência e a segurança das operações. Planejamento adequado, escolha correta de materiais, conformidade com normas de segurança, comunicação eficaz, testes finais, treinamento da equipe e documentação do processo são aspectos essenciais que devem ser considerados. Ao seguir essas diretrizes, as empresas podem minimizar riscos e garantir que suas instalações sejam bem-sucedidas.
Em conclusão, a manutenção e instalação industrial são fundamentais para garantir a eficiência e a segurança nas operações. Ao evitar erros comuns, como a falta de planejamento, a escolha inadequada de materiais e a ignorância das normas de segurança, as empresas podem otimizar seus processos e prolongar a vida útil dos equipamentos. Investir em treinamento, comunicação eficaz e documentação adequada também são práticas essenciais que contribuem para o sucesso das instalações. Com as orientações apresentadas, é possível garantir que sua instalação industrial funcione de maneira otimizada, promovendo um ambiente de trabalho seguro e produtivo.